ADVANTAGES, FEATURES & BENIFITS
- Can be used on green (fresh) and cured concrete.
- Provides long-lasting internal waterproofing and moisture blocking from positive and negative sides.
- Reduces water permeability through concrete by 2-3 orders of magnitudes when tested @ 200 psi (1.38 MPa) according to CRD-48-92.
- Provides concrete surface with Hydrophobicity characteristics: Excellent water-repelling properties that help prevent water, jet fuel, and oil from wetting and saturating concrete surfaces: PAVIX increases water contact angle for concrete surfaces by greater than 90°, see Fig. 1).
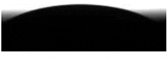
|
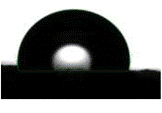 |
Low Contact Angle
|
High Contact Angle (105o)
|
Fig. 1: Water contact angles for concrete surfaces comparing control (left) & Pavix-treated (right) using TX-DOT pavement mix design at w/c ratio=0.47
|
- Reduces damages from Alkali-Silica Reactions (ASR) and silicate dusting (see Table 1).
Table 1: Percentage reduction in length change due to ASR according to ASTM C1567 using Iowa DOT C4-WRC20 concrete mix design at various w/c ratios |
Type of Aggregate |
w/c ratio
|
0.39
|
0.43 |
0.47
|
Non-Reactive (Ames Mine) |
43
|
42 |
26
|
Reactive (Platte River) |
28
|
20 |
24
|
- Reduces ice adhesion (shear testing) by up to 90% (see Fig. 2) and hence reduces the consumption of deicing salts by 50-60%.

Fig. 2: Ice Adhesion Test Results comparing control (blue) & PAVIX-treated (red) using TX-DOT pavement mix design at w/c=0.43 using Modified Direct Shear Apparatus (Geocomp SheraTrac-II)
- Reduces damage caused by repeated freezing & thawing cycles (see Fig. 3).
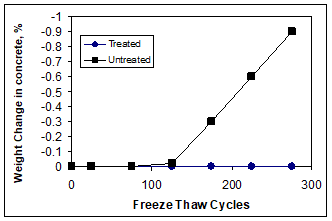
Fig. 3: ASTM C666-97: Freezing & thawing effect on treated & untreated when PAVIX applied on cured concrete samples
- Reduces penetration of chloride ions from de-icing salts & increases concrete electrical resistivity by a percentage over 90% (see Table 2).
Table 2: Total charge passed & percentage reductions from results using ASTM C1202 on Iowa DOT C4-WRC20 Concrete Mix Design with w/c ratio=0.4 |
Parameter |
Control |
PAVIX @ NaCl Side |
PAVIX @ NaOH Side |
PAVIX @ Both Sides (NaOH & NaCl) |
Charge Passed (Coulombs) |
646
|
13 |
18 |
60
|
% Reduction |
|
98% |
97% |
90%
|
- Minimizes concrete scaling due to freezing and thawing in the presence of deicing chemicals (see Fig. 4-a & Fig. 4-b).
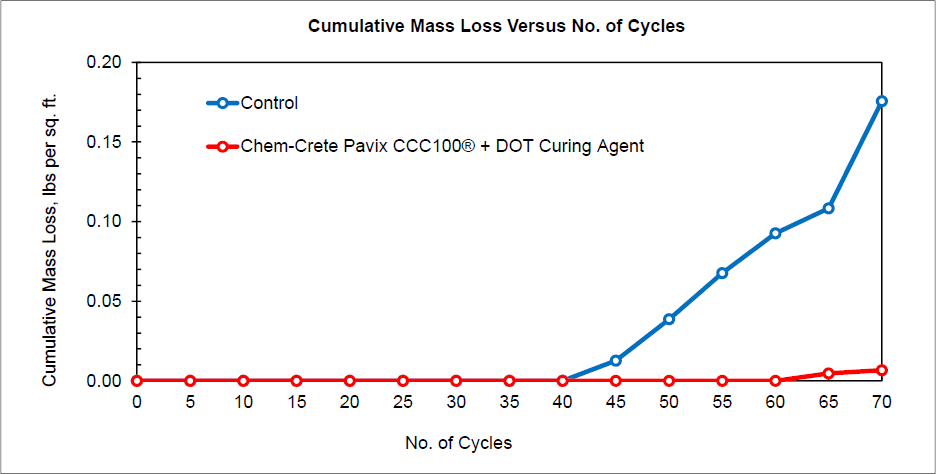
Fig. 4-a: ASTM C672-98: scaling resistance when PAVIX is applied on green concrete surfaces
exposed to deicing chemicals, this test shows 94% reduction in mass loss at 70 Freeze-Thaw cycles.
Control sample without PAVIX and curing compound
|
Sample with PAVIX and curing compound
|
Fig. 4-b: concrete lab samples show scaling effect on PAVIX treated and untreated concrete surfaces after 70 cycles of freezing & thawing |
- Protects reinforcing steel bars against corrosion without negative effects on existing steel cathodic protection.
- Self-healing: seal cracks up to 1/16th inch (1.5 mm).
- Prevents or minimizes early joint failure or deterioration.
- Maximizes joint sealant adhesion by reducing moisture content.
- Helps concrete stay whiter & brighter (Albedo Surface).
- Eliminates fungal and microbial growth according to anti-fungal and microbial test method MIL-SDD810G.
- Increases concrete density of high porosity concrete specimen by 6-7 % (TX DOT mix-design, w/c=0.5 using ASTM C642-9).
- Increases coating adhesion by 13% (ASTM D7234 using high porosity, moderate-strength laboratory concrete specimen, w/c=0.48).
- 100% green, environmentally friendly, safe & non-toxic.
- Can be applied vertically, horizontally and overhead.
- Reduce the consumption of deicing materials by greater than 50%.
TECHNICAL
Physical Properties @ 77 oF (25 oF)
Specific Gravity |
1.1 – 1.2 |
Viscosity |
2.4 centipoises |
Freezing Point |
25ºF (-3.89°C) |
Boiling Point |
219ºF (104 °C) |
Color |
Clear |
Environmental Hazards |
None |
Drying Time |
2 – 3 hours |
Odor |
None |
Toxicity |
None |
Fumes |
None |
Flammability |
None |
Product Performance: PAVIX is tested according to the following test standards:
- CRD-48-92 US Army Corps of Engineers Standard Test Method for Water Permeability of Concrete
- ASTM D6489-99 Determining the Water Absorption of Hardened Concrete Treated with a Water Repelling Coating.
- ASTM C642-97 Standard Test Method for Density, Absorption, and Voids in Hardened Concrete
- ASTM C1202-91 Electrical Indication of Concrete’s Ability to Resist Chloride Ion Penetration.
- AASHTO T260 Sampling and Testing for Chloride Ion in Concrete and Concrete Raw Materials
- AASHTO T277 Electrical Indication of Concrete’s Ability to Resist Chloride Ion Penetration
- AASHTO T259-00 Resistance of Concrete to Chloride Ion Penetration
- ASTM C1218 Water-Soluble Chloride in Mortar and Concrete.
- ASTM C672-98 Scaling Resistance of Concrete Surfaces Exposed to Deicing Chemicals
- ASTM C457-98 Microscopical Determination of Parameters of the Air-Void System in Hardened Concrete
- MIL-STD-810G Fungal Resistance According to Test Method Standard for Environmental Engineering Considerations and Laboratory Tests
- ASTM D4541-95 Pull-Off Strength of Coatings Using Portable Adhesion Testers
- ASTM C1583 Bond Strength or Tensile Strength of Overlay Materials by Direct Tension
- ASTM F609-96 Standard Test Method for Using a Horizontal Pull Slipmeter (HPS)
- ASTM E303-93 Measuring Surface Frictional Properties Using the British Pendulum Tester
- ASTM D7234 Standard Test Method for Pull-Off Adhesion Strength of Coatings on Concrete Using Portable Pull-Off Adhesion Testers
- ASTM C666-97 Resistance of Concrete to Rapid Freezing & Thawing
- ASTM C1567 Standard Test Method for Determining the Potential Alkali-Silica Reactivity of Combinations of Cementitious Materials and Aggregate (Accelerated Mortar-Bar Method)
APPLICATION
Limitations: Do not apply PAVIX in the following cases:
- If the concrete surface temperature falls below 40°F (5°C).
- If the area has been previously treated with sealing agents unless the sealers are removed by chemical or mechanical means.
Application:
Fully cured or existing concrete: Repair and seal joints, cracks, and voids greater than 1/16th inch prior to the application. Concrete surfaces must be clean and sound prior to application of the product. Proper cleaning will open the surface pores and capillaries to enhance the penetration process. Compressed air or mechanical sweepers can be used to remove dust and loose particles from the surface. Flushing the area to be treated with water can improve the cleaning process. However, for heavily contaminated areas special concrete cleaning agents such as Chem-Crete CONCLEAN CCC060 can be used to remove dirt, grease, and oil from those areas.
Broom finished concrete should be lightly dampened (NO STANDING WATER) prior to application to eliminate potential overlap lines.
Coverage: Apply at an average coverage rate of 150-200 ft2/gal (3.7-4.9 m2/liter) in one coat.
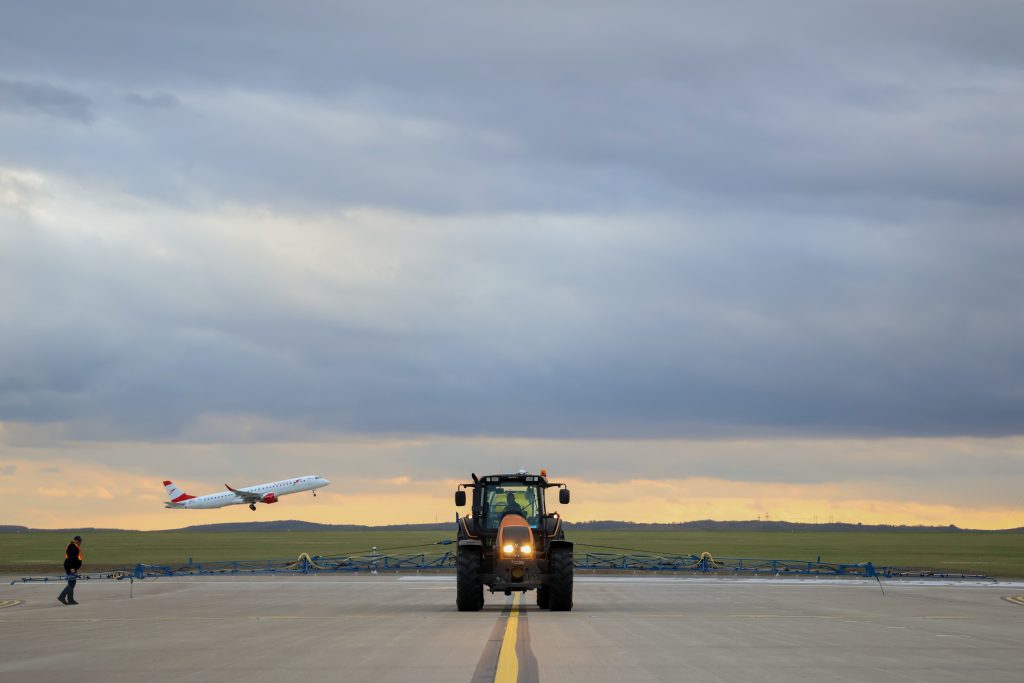
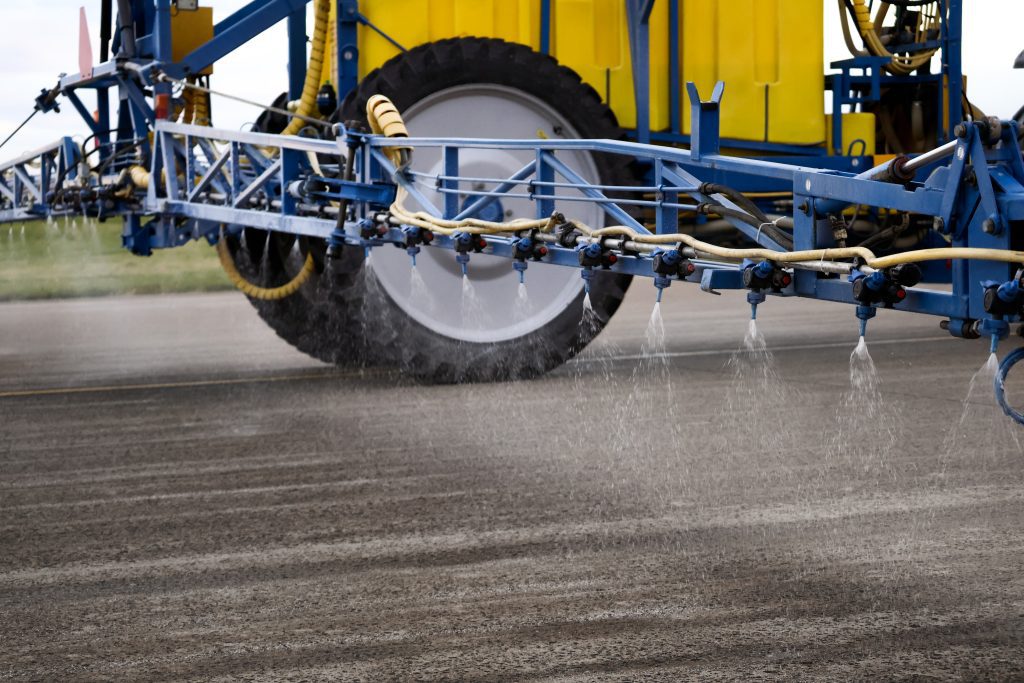
Green/Plastic Concrete:
- Only consider an application when concrete finishing is completed and the disappearance of bleed water.
- Concrete should not be in duress and should be curing normally.
- Apply PAVIX uniformly and at an average coverage rate of 200 ft2/gallon (4.9 m2/L).
- DO NOT allow the PAVIX to puddle or pool.
- Application of membrane-forming curing compound within 20 minutes from the initial PAVIX application.
- Apply the membrane curing compound at the manufacturer’s recommended coverage rate.
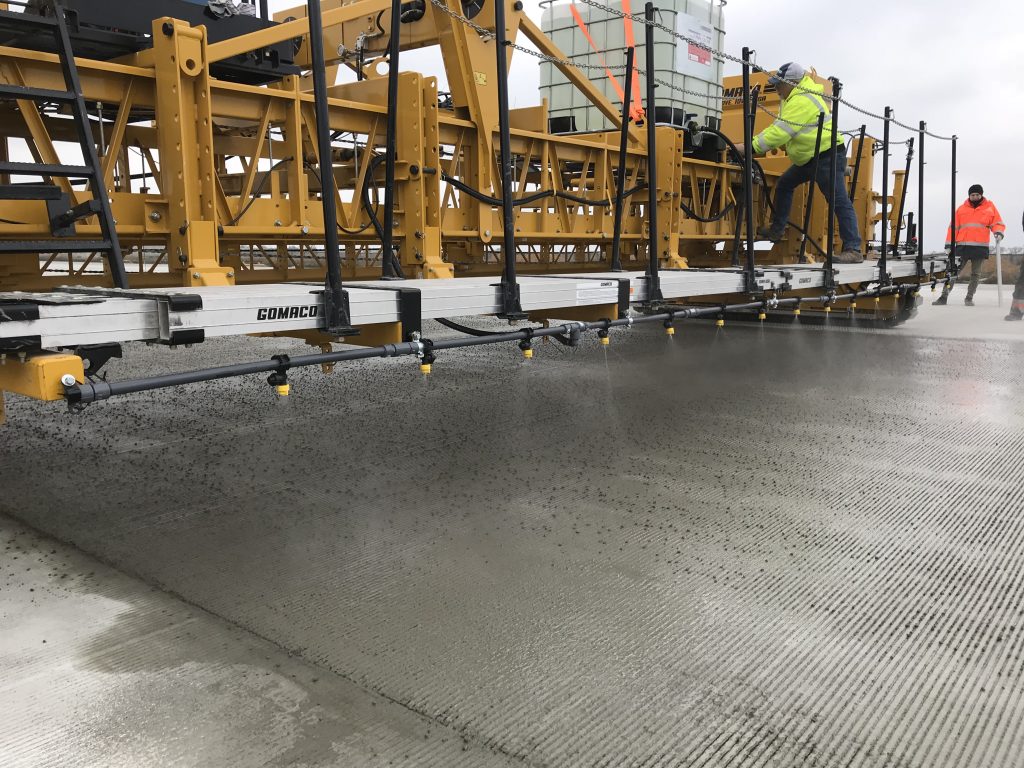
Cleaning: all tools and equipment must be cleaned with clean water immediately after use.
STORAGE
Two-year shelf life when stored in its original, unopened container in a cool, dry place. Always agitate the product before using. DO NOT ALLOW PRODUCT TO FREEZE. Repeated freezing and thawing may cause damage to the product.
SAFETY
As with all construction chemical products, adequate precautions and care must be taken during usage and storage. Avoid direct contact with foodstuff, eyes, skin, and mouth. Any contacted areas should be washed thoroughly with clean running water and soap.
Always wear protective goggles and gloves. In case of eye contact, flush for fifteen minutes with warm water. If eye irritation persists, seek medical attention. In case of ingestion or swallowing, drink 2 glasses of clean water and seek medical attention. KEEP OUT OF REACH OF CHILDREN.
WARRANTY
LIMITED WARRANTY: International Chem-Crete warrants that, at the time and place we make shipment, our materials will be of good quality and will conform to our published specifications in force on the date of acceptance of the order.
DISCLAIMER: The information contained herein is included for illustrative purposes only, and to the best of our knowledge, is accurate and reliable. International Chem-Crete cannot, under any circumstances, make any guarantee of results or assume any obligation or liability in connection with the use of this information.
As International Chem-Crete has no control over product usage, it is recommended that the product be tested to determine suitability for a specific application and/or that our information is valid in a particular circumstance. Responsibility remains with the architect or engineer, contractor and owner for the design, application and proper installation of each product. Specifier and user shall determine the suitability of products for specific application and assume all responsibilities in connection therewith. Any liability is limited to the replacement of material if proven faulty. AM010322-05
GALLERY
Runway Application
Oprav Malacky Airport, Czech Republic
Bridge Application
Branson, Missouri State. USA
Bridge Application
Amarillo, Texas. USA
Bridge Application
Collins Bridge – Richardson, TX USA